对750 ℃不同热处理时间2205双相不锈钢析出相的定性定量分析
时间:2019-06-13
作者:无锡不锈钢板
浏览:0
摘要: 经过等温热处理,双相不锈钢中铁素体在向奥氏体转变的过程中通常会形成碳化物相、金属间相、氮化物析出相等。这些析出相在合金中形成将导致不锈钢的脆化,显著降低钢的塑性、韧性和耐蚀性。为了对750 ℃不同热处理时间双相不锈钢析出相做定性定量分析,本实验首先研究了不同电解体系下双相不锈钢的电解效果,在选择好合适的电解制度后,利用电解分离方法将析出相从基体中分离。通过扫描电镜(SEM)和X衍射(XRD)定性研究了提取后析出相的形貌以及结构特性的变化过程;并利用激光粒度仪分析了析出相的粒度分布变化趋势。此外,利用氧氮仪分析仪测定了析出相的氮含量;利用碳硫分析仪测定了残渣经酸处理后的碳含量。最后,通过电感耦合等离子光谱)ICP)检测化学分离后溶液中合金元素的含量,并结合氮和碳含量的数据,计算不同析出相的元素组成及含量,最后讨论了750℃下不同热处理时间对析出相的影响,在时效开始时先形成金属间相χ相,随着时间的延长,χ相减少,而σ相逐渐形成并最终占主量。
关键词:双相不锈钢,金属间相,热处理,定性定量分析
双相不锈钢以其良好的耐氯化物腐蚀和耐点蚀性能、较高的力学性能等特点,以及较低制造成本的优势,取代目前不耐腐蚀的构件和一些常用的高铬镍不锈钢结构件是完全可能的,因而其会在海洋工程、海洋钻井平台、舰船及东南沿海地区武装装备方面具有重大的应用前景[1]。双相不锈钢研究的难点之一在于一些有害析出相的含量控制,如σ相、χ相等金属间相硬而脆在合金中形成将导致合金的脆化,显著降低钢的塑性、韧性和耐蚀性;不同粒径大小及数量的Cr2N析出影响不锈钢的耐腐蚀性能和冲击韧性。此外,析出相大小也严重影响材料的力学性能,如对高温蠕变、疲劳性能以及其裂纹扩展速率等。因此,有效地定量分析双相4不锈钢中的析出相,对于改善双相不锈钢的性能,研究材料合金化机理,选择合适的热处理制度,高牌号双相不锈钢产品的研制与开发都有十分重要的意义。
当前,双相不锈钢相分析的方法很多[2-10],这些分析技术各有特点和局限性。由于析出相的各个特征都很重要,所以各种相分析手段常常需要互相配合应用,才能得到较为准确可靠的结果。为了对750 ℃不同热处理时间2205双相不锈钢析出相做定性定量分析,本实验首先研究了不同电解体系下双相不锈钢的电解效果,在选择好合适的电解制度后,利用电解分离的方法将750 ℃下不同热处理时间的析出相从基体中分离出来。通过SEM和XRD定性研究了析出相的形貌以及结含量。最后,通过ICP检测化学分离后溶液中正离子的浓度并结合氮和碳含量的分析计算不同析出相的含量的元素组成。
1 实验方法
1.1 实验材料及热处理制度
实验所用的2205双相不锈钢的成分见表1所示,所有的实验试样均先在1 050 ℃下固溶处理后进行不同的回火处理。其中1号样品为直接固溶处理后的试样,2~6号分别为样品经750 ℃等温热处理1 h、2 h、5 h、7 h,24 h。
表1 2205双相不锈钢的化学成分
Table 1 Chemical composition of 2205 duplex stainless steel
元素Element
|
C
|
Si
|
Mn
|
P
|
S
|
Cr
|
Mo
|
Ni
|
N
|
含量Content(w/%)
|
0.024
|
0.62
|
1.4
|
0.023
|
0.001
|
21.07
|
3.01
|
5.36
|
0.155
|
1.2 仪器与试剂
F34-EH冷阱(德国Julabo公司);273A/10A电化学综合分析仪(美国Princeton Applied Research公司);Mastersizer 2000激光粒度仪(英国 Malvern公司);IRIS Intrepid Ⅱ电感耦合等离子发射光谱仪(美国Thermo公司);RINT2500/PC X射线衍射能谱仪(日本理学);Axioplan2金相显微镜(德国蔡氏公司);S-4200扫描电镜(日本HITACHI公司);TC600氧氮分析仪(美国Leco公司);444LS碳硫分析仪(美国Leco公司);
1.3 实验过程
试样的制备:进行物理化学相分析时,将试样精车成Φ10×100 mm的圆棒,极化曲线绘制时,试样线切割成Ф10×1 mm的薄片并磨成镜面;金相以及扫描电镜分析时,将试样制成10×10×5 mm的小块,将待观察面磨成镜面,用400 g/L苦味酸乙醇溶液腐蚀后进行分析。
极化曲线的绘制:所需的电解液加入烧瓶后,将试样固定在试样夹具上作为工作电极,带盐桥的氯化钾饱和甘汞电极为参比电极,铂丝为对电极;待几个电极固定好后,将整套装置放入温度为-10 ℃的冷阱中。
析出相的提取与收集方法:带盐桥的氯化钾饱和甘汞电极为参比电极,铂丝为对电极,圆棒状试样为工作电极,分别与仪器上对应的导线相连;待几个电极固定好后,将整套装置放入冷阱中进行恒电流电解。电解结束后将试样棒取出放入装有乙醇的烧杯里超声后用0.02 μm的亲油滤膜抽真空过滤,并用乙醇洗净真空干燥。
析出相的粒度检测:析出相残渣通过过滤及超声分散后,在醇溶液中用激光粒度仪对电解残渣进行粒度分布检测。该方法具有测量速度快、动态范围大(0.02~2 000μm)、操作简便、重复性好等优点。
析出相的氮含量检测:需要在检测方法中添加试样预处理环节,通过试样预处理先将滤膜中的氮除尽。样品中的氮以氮分子的形式释放出来,试样气流经稀土氧化铜时,一氧化碳全部转化为二氧化碳。检测后,碱石棉吸收二氧化碳,干燥剂吸收水,以避免干扰热导的检测。最后,试样气流流过热导池测定氮。
析出相的碳含量检测:为了降低过滤介质的本底浓度,本实验将酸洗石棉先进行高温灼烧,冷
却后用硝酸加热清洗,并加入一定的硫酸冒烟。处理好用清水清洗干净后烘干,而后在马弗炉中高温灼烧。将电解后的析出相残渣经过酸处理后用酸洗石棉过滤,而后将残渣与石棉在150 ℃的烘箱中干燥3~4 h,该实验所用的器皿均要进行去碳处理。试样在充有氧气流的高频感应炉内在催化剂的助熔下加热获得的高温燃烧,把样品中的碳转化成一氧化碳、二氧化碳的混合物,该混合物由氧气流传输经过镀铂硅胶时,一氧化碳被氧化至二氧化碳,通过红外吸收法测定由氧气流传输的二氧化碳浓度。
析出相的化学分离与成分检测:采用HCl-H2O2体系将Cr2N与金属间相溶解,过滤后的残渣经过碱熔定量便可得到碳化物的正元素组成与含量,而溶液的ICP定量分析结果扣除去Cr2N中Cr的含量,余者便为金属间相的组成与含量。
2 结果与讨论
2.1 合适的电解条件的选择
2.1 合适的电解条件的选择
不锈钢中含有较高的Cr、Ni, 溶液中很容易钝化, 而且钢中含有的碳化物及金属间化合物大都比较稳定, 所以电解液的酸度应该比较大, 活性离子含量也应较高, 在水溶液中进行电解是比较困难的,如果用醇做溶剂, 对基体活化溶解的效果更好,同时可以抑制一些相的水副反应的发生,并使电解后的表面光滑,从而减少损失,便于洗涤。试验首先考查了试样棒2号在六种不同电解制度下(电解液不同,但均以醇为溶剂)的极化曲线(图1)。即利用析出相与基体在电解液中稳定电位的差别,外加电流使试样极化,当极化条件合适(即电极电位介于基体的稳定电位与析出相稳定电位之间),合金基体以一定的速度电解,目的相则以不溶性残渣的形式被提取出来。图1显示腐蚀电流从大到小分别为电解制度4-5-2-6-1-3。因此,电解制度6,1,3的电解速度相对要慢。电解效果也证明了2205双相不锈钢在电解制度2,4,5中的电解效果比较好。而电解制度3和6的均出现明显的点蚀现象。
从电解效果来看,在电解制度2,4,5中试样2号在0.5 A电流下电解3 h试样的质量损失均在1.5 g左右,说明基本符合电解中电荷平衡。通过电解残渣的XRD定性分析来进一步确定其分离效果,从图2的XRD结果可知,在电解液2中可得到金属间相+Cr2N相,而在电解液5中除了得到金属间相+Cr2N相外还有部分的铁素体和奥氏体残留。特别是在电解液4号下残渣含有大量的基体,且其强度掩盖了其他析出相的强度值。此外,通过原试样棒(未敏化处理)在电解液2下没有得到任何残渣,也进一步说明了该电解制度的提取效果。
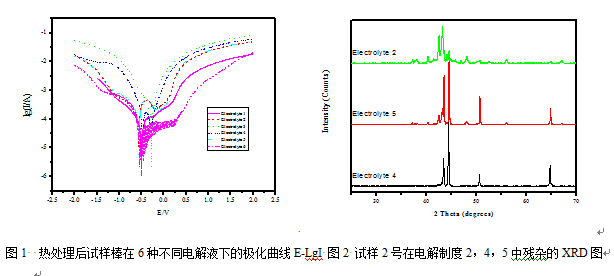
2.2 析出相的形貌观测
双相不锈钢在300 ℃以上时组织会产生初始奥氏体、铁素体以外的二次相,从而使其抗蚀性及其机械性能受到损害,这是双相不锈钢生产和使用过程中遇到的一个普遍问题。从实验的结果(图3)来看,没有时效处理的试样在晶间和晶内均无析出相存在,而样品2号在晶界和铁素体内都有明显析出相形成。表明在考察的时效温度下,随着时效时间的延长,铁素体相在向奥氏体转变,同时伴随着晶界和铁素体内部析出相的析出。为了考查电解前后析出相形貌的一致性与电解后析出相的微观观测,我们将电解残渣进行分散后用扫描电镜观测,图4是试样5号和6号电解残渣的扫描电镜照片,粒径从几百个纳米到几个微米不等,且通过超声震荡可以得到较好的分散性。
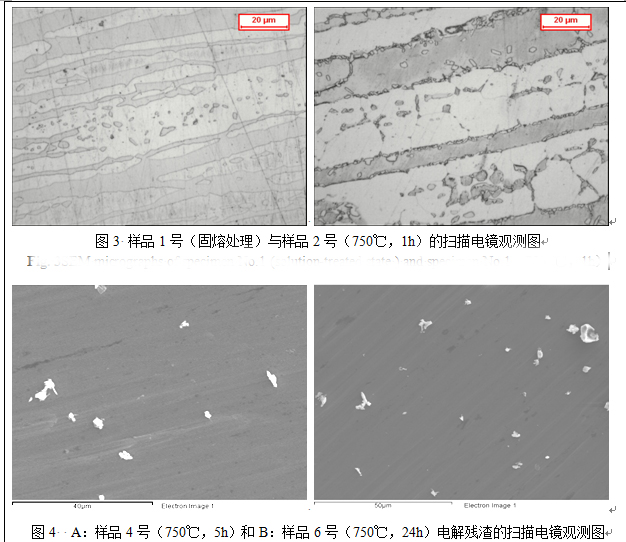
图5是试样在750 ℃时效不同时间电解残杂的XRD图谱,反映了在同一时效温度下,随着时间的延长,析出相的形成和变化。在时效1 h后,析出相主要是以M23C6和Cr2N为主,并有少量的χ相;到2 h,χ相开始增多;5 h以后则有部分σ相出现,而后伴随着时间的延长,σ相越来越多,相应χ相开始减少,到24 h时,σ相已经占主导地位,且形成的晶体很完整,XRD图谱峰和清晰明显。该过程可以描述为:M23C6,Cr2N,χ相→χ相,Cr2N,M23C6→χ相,Cr2N,σ相→σ相,χ相。M23C6的析出导致相界附近的铁素体相内铬的损失,铁素体内的贫铬促进原始α/γ相界向铁素体晶内迁移,释放出多余的铬给邻近的铁素体相,为金属间相形核创造了条件[11-12]。图6是 750 ℃下不同时效时间电解残渣的SEM观测,通过能谱分析可知,图中针状(刺状)的部分主要是含Fe, Cr, Mo,不含Ni;而块状的部分主要含Fe, Cr, Mo, Ni, Si,初步可认定其为σ相。该SEM图的表征与图6中XRD定性的结果相吻合,显示了金属间相从χ相到σ相的变化,图6A为750 ℃下时效1 h,此时的金属间相为针状(刺状)的χ相;而图6B为750℃下时效5 h,此时的金属间相以χ相为主,同时含σ相;图6C是750 ℃下时效24 h,金属间相以σ相为主,同时含少量的χ相。从SEM的检测可知,在同时含χ相和σ相的过渡阶段,χ相和σ相并不是独立分开的,两者是共存的,可以初步认定σ相是在χ相的基础上形成的。而图6D,7E分别是针状(刺状)和块状区域的能谱图,前者主要是含Fe, Cr, Mo,不含Ni;而后者主要含Fe, Cr, Mo, Ni, Si,。
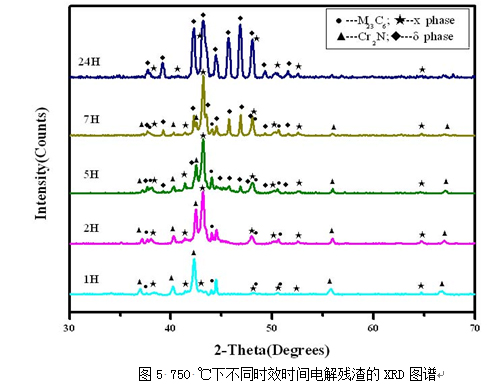
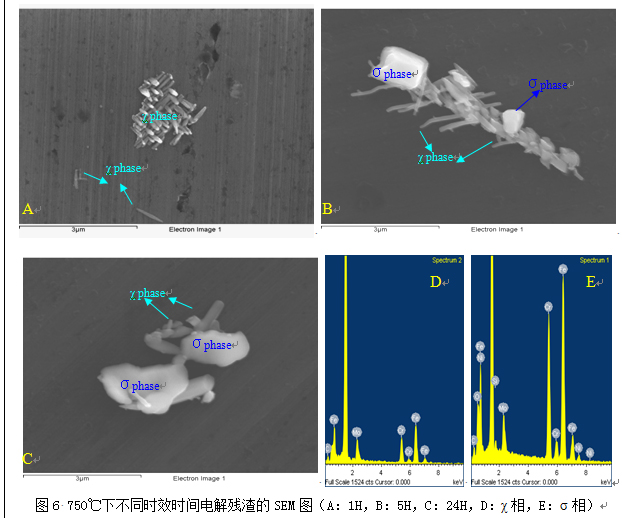
2.4 不同热处理时间下析出相总氮含量测定
氮化物析出影响不锈钢的耐腐蚀性能和冲击韧性,因此氮化物析出相的含量测定对研究2205双相不锈钢的性能有着重要的作用。通过XRD结构分析知道,析出相中的氮化物为Cr2N,通过测定析出相中氮总量除以电解量可以得到不同回火条件下析出相中氮的百分含量。为了避免回火过程中的增氮,实验考察了试样在不同回火温度和时间下的氮含量,发现氮的含量并没有显著的变化,多次测量结果的平均在0.154-0.157 %之间,因此可以证明试样在回火处理的过程中没有出现增氮和逸氮的现象。通过氧氮分析仪对电解残渣含氮量的测定可以得到不同回火温度和时间下氮化物析出相的氮含量(见图7),氮化物的析出主要在600-850 ℃之间,从样品的析出相氮含量分析可知,在750 ℃回火下氮化物析出明显,析出相中氮占电解失重的量为0.015 % 至 0.025 %,而且随着回火时间的增加,析出相总氮含量先增大后减小,而当温度在850℃时,随着回火时间的增加,氮化物析出相呈明显下降的趋势,特别是到950℃回火,氮化物析出相当少。图8显示,在电解条件一致的情况下,不同时效时间样品的电解量变化不大(750 ℃时介于0.70—0.74之间)。而在考查的时效时间范围内,析出相的百分含量随时间的延长呈明显上升的趋势(从1小时的0.93 %逐渐上升到7小时的5.08 %),根据氮的分析结果可知在该时效条件下氮含量变化并不明显,因此,随时效时间的延长,金属间相含量有显著的增加。
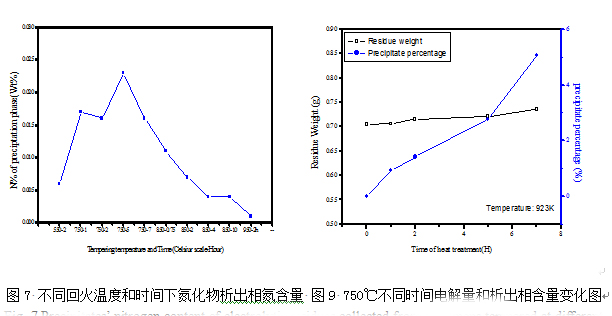

2.5 不同热处理时间下析出相总碳含量测定
表2 不同回火温度和时间下试样电解残渣的总碳含量列表
时效温度-时间
Aging temperature-time
|
电解失重(g)
electrolysis loss (g)
|
碳含量(%)
Carbon (%)
|
平均值(%)
Average(%)
|
固熔态
Solution-treated state
|
0.4535
|
0.0055
|
0.006
|
0.4611
|
0.0057
|
||
650 ℃-2 h
|
0.4528
|
0.0199
|
0.021
|
0.4752
|
0.0217
|
||
750 ℃-1 h
|
0.4678
|
0.0155
|
0.017
|
0.4700
|
0.0178
|
||
750 ℃-2 h
|
0.4698
|
0.0193
|
0.019
|
0.4769
|
0.0182
|
||
750 ℃-5 h
|
0.4754
|
0.0255
|
0.025
|
0.4618
|
0.0246
|
||
750 ℃-24 h
|
0.4980
|
0.0243
|
0.024
|
0.4902
|
0.0239
|
双相不锈钢含C量很低,碳化物起的作用较小。然而碳化物的析出仍然是可能的,在950 ℃以下会迅速析出M23C6,而在950~1050 ℃之间则会析出M7C3[13],值得注意的是碳化物的析出会促进σ相之类有害相的形成。本实验拟通过电解残渣测总碳的方法考察碳化物析出物中碳含量。表2是不同试样的碳测定数据,从中可以看出固熔处理后试样电解残渣(量极少)的碳含量为0.006 %,回火650 ℃-2 H试样电解残渣的碳含量为0.021 %。而对于750℃回火不同时间试样电解残渣的碳含量从1 h的0.017%逐步上升至5 h的0.024 %(与原试样碳含量相等),并保持稳定,说明碳化物在回火时很快形成,对于750℃回火下,试样在5小时后绝大多数都析出。
2.6不同热处理时间下金属间相的含量和元素组成
基于从XRD的结果可知,在所研究回火条件下的电解残渣中的N均以Cr2N的形式存在,故实验采用HCl-H2O2体系将Cr2N与金属间相溶解,过滤后的残渣经过碱熔定量便可得到碳化物的正元素组成与含量,而溶液的ICP定量分析结果扣除去Cr2N中Cr的含量,余者便为金属间相的组成与含量。图9显示的是750 ℃回火不同时间试样的不同析出相的组成与元素含量,从中可以看到,随着回火时间的延长,金属间相的含量呈明显上升的趋势,从1 h的0.547%上升到24 h的5.802%。金属间相富含Fe,Cr,Mo,并且含有少量的Ni,Mn,Si,而碳化物相Cr,Fe为主,不含Ni,Mn元素。此外,由于χ相是富钼的相,不含Ni元素,而σ相含少量的Ni元素,因此可以通过这两种元素的含量来衡量χ相和σ相的变化。在时效1 h,金属间相几乎不含镍,且元素百分含量Cr:Fe:Mo接近2:4:3,而在5 h,该比值接近2:4:2,到7 h,该比值接近2:4:1。该变化与XRD的分析相吻合,即在时效开始时先形成金属间相χ相,而随着时间的延长,σ相逐渐形成并最终占主量。
3 结论
(1)实验首先研究了不同电解体系下双相不锈钢的电解效果,在选择好合适的电解制度后,利用电解分离的方法将750 ℃下不同热处理时间的析出相从基体中分离出来。通过SEM和XRD定性研究了析出相的形貌以及结含量。最后,通过ICP检测化学分离后溶液中正离子的浓度并结合氮和碳含量的分析计算不同析出相的含量的元素组成。
(2)750 ℃时效1 h后,析出相主要是以M23C6和Cr2N为主, 到2小时,χ相开始形成;5 h以后则有部分σ相出现,而后伴随着时间的延长,σ相越来越多,相应χ相开始减少,到24 h时,σ相已经占主导地位,且形成的晶体很完整,XRD图谱峰和清晰明显。
(3)2205双相不锈钢的析出相主要是在晶界分布,随着时效温度的升高及时间的延长,铁素体在向奥氏体转变的过程中在铁素体内部也有金属间相生成,而氮化物以Cr2N为主,主要在600-850 ℃形成;
(4)实验考查了750 ℃回火不同时间试样的不同析出相的组成与元素含量,从中可以看到,随着回火时间的延长,金属间相的含量呈明显上升的趋势,从1H时的0.547 %上升到24H的5.802 %。在时效开始时先形成金属间相χ相,而随着时间的延长,σ相逐渐形成并最终占主量。
参考文献:
[1Michalska J, Sozanska M. Qualitative and quantitative analysis of sigma and gamma phases in 2205 duplex stainless steel[J]. Materials Characterization, 2006, 56(4-5): 355-362.
[2] Garz′on C M, Tschiptschin A P. EBSD texture analysis of a high temperature gas nitrided duplex stainless steel[J]. Materials Science and Engineering A, 2006, 441: 230-238.
[3] Nelson D E, BneslackⅢ W A, Lippold J C. Characterization of the weld structure in a duplex stainless steel using color metallography[J]. Materials Characterization, 1997,39: 467-477.
[4] Michalska J, Sozanska M. Selective etching of phase and structural constituents in duplex stainless[C]. Proc Mass and Charge Transport in Materials Summer School, Krakow, Poland, 2004, 6: 77-83.
[5] Dhua SK, Ray A. Microstructural manifestations in color: some applications for steels[J]. Materials Characterization, 1996, 37: 1-9.
[6] Michalska J, Sozanska M. Qualtative and quantitative analysis of α and χ phases in 2205 duplex stainless steel[J]. Materials Characterization 2006, 56: 355-362.
[7] Liou H Y, Hsieh R , Tsai W T. Microst ructure and pitting corrosion in simulated heat affected zones of duplex stainless steels[J]. Mater Chem Phys ,2002 ,74 (1) : 33-42.
[8] Lai J K L , Shek C H , Shao Y Z. Magnetic properties of thermal aged 316 stainless steel and it’s precipitated phases[J]. Mater Sci Eng A , 2004, 379 (122) : 308-312.
[9] Chino A, Ihida M, Iwata H, Determination and Precipitation Behavior of sigma -Phase, Carbides and Nitrides in Duplex Stainless Steels[J]. Tetsu-to-Hagane (J. Iron Steel Inst. Jpn.). 1989, 75, 10: 1936-1942.
[10] Miao Lede, Zhang Yi, Wang Zhiyu. Electrochemical extraction and the analysis of intermetallic phases and nitrides in tempered duplex stainless steels[J], Baosteel Technical Research, 2009, 3(2): 52-57.
[11] Kuroda T. Precipitation behavior of σ phase in duplex stainless steels and weld metals[J]. Welding in the World, 2000, 44(2): 17-23.
[12] Lee C, Cho H, Choi D. Effect of isothermal treatment of SAF 2205 duplex stainless steel on migration of δ/γ interface boundary and growth of austenite[J]. Mater Charact, 1999, 285: 156-161.
[13] Karlsson L. Intermetallic phase precipitation in duplex stainless steel and weld metals[J], WRC Bulletin, 1999, 438 :1-5.
(2)750 ℃时效1 h后,析出相主要是以M23C6和Cr2N为主, 到2小时,χ相开始形成;5 h以后则有部分σ相出现,而后伴随着时间的延长,σ相越来越多,相应χ相开始减少,到24 h时,σ相已经占主导地位,且形成的晶体很完整,XRD图谱峰和清晰明显。
(3)2205双相不锈钢的析出相主要是在晶界分布,随着时效温度的升高及时间的延长,铁素体在向奥氏体转变的过程中在铁素体内部也有金属间相生成,而氮化物以Cr2N为主,主要在600-850 ℃形成;
(4)实验考查了750 ℃回火不同时间试样的不同析出相的组成与元素含量,从中可以看到,随着回火时间的延长,金属间相的含量呈明显上升的趋势,从1H时的0.547 %上升到24H的5.802 %。在时效开始时先形成金属间相χ相,而随着时间的延长,σ相逐渐形成并最终占主量。
参考文献:
[1Michalska J, Sozanska M. Qualitative and quantitative analysis of sigma and gamma phases in 2205 duplex stainless steel[J]. Materials Characterization, 2006, 56(4-5): 355-362.
[2] Garz′on C M, Tschiptschin A P. EBSD texture analysis of a high temperature gas nitrided duplex stainless steel[J]. Materials Science and Engineering A, 2006, 441: 230-238.
[3] Nelson D E, BneslackⅢ W A, Lippold J C. Characterization of the weld structure in a duplex stainless steel using color metallography[J]. Materials Characterization, 1997,39: 467-477.
[4] Michalska J, Sozanska M. Selective etching of phase and structural constituents in duplex stainless[C]. Proc Mass and Charge Transport in Materials Summer School, Krakow, Poland, 2004, 6: 77-83.
[5] Dhua SK, Ray A. Microstructural manifestations in color: some applications for steels[J]. Materials Characterization, 1996, 37: 1-9.
[6] Michalska J, Sozanska M. Qualtative and quantitative analysis of α and χ phases in 2205 duplex stainless steel[J]. Materials Characterization 2006, 56: 355-362.
[7] Liou H Y, Hsieh R , Tsai W T. Microst ructure and pitting corrosion in simulated heat affected zones of duplex stainless steels[J]. Mater Chem Phys ,2002 ,74 (1) : 33-42.
[8] Lai J K L , Shek C H , Shao Y Z. Magnetic properties of thermal aged 316 stainless steel and it’s precipitated phases[J]. Mater Sci Eng A , 2004, 379 (122) : 308-312.
[9] Chino A, Ihida M, Iwata H, Determination and Precipitation Behavior of sigma -Phase, Carbides and Nitrides in Duplex Stainless Steels[J]. Tetsu-to-Hagane (J. Iron Steel Inst. Jpn.). 1989, 75, 10: 1936-1942.
[10] Miao Lede, Zhang Yi, Wang Zhiyu. Electrochemical extraction and the analysis of intermetallic phases and nitrides in tempered duplex stainless steels[J], Baosteel Technical Research, 2009, 3(2): 52-57.
[11] Kuroda T. Precipitation behavior of σ phase in duplex stainless steels and weld metals[J]. Welding in the World, 2000, 44(2): 17-23.
[12] Lee C, Cho H, Choi D. Effect of isothermal treatment of SAF 2205 duplex stainless steel on migration of δ/γ interface boundary and growth of austenite[J]. Mater Charact, 1999, 285: 156-161.
[13] Karlsson L. Intermetallic phase precipitation in duplex stainless steel and weld metals[J], WRC Bulletin, 1999, 438 :1-5.